Lean Optimization
The avoidance of waste (MUDA) in a processes, is essential for optimization according to LEAN. The former Toyota chief engineer Taiichi Ohno once defined seven forms of Muda, which must be recognized and avoided on the way to efficient production.
Around this basic idea, various optimization methods were subsequently developed according to the so-called Toyota Production System (TPS), whose consistent application, but also their constant questioning and review, help to make production processes efficient.
In the past, Tecoma uses LEAN Management in combination with TOC, after determining the constraints in the process with Value Stream Mapping (VSM) we solve them and support the environment with implementing various LEAN Methodes. With this method we already achieved throughput increases of >70%:
With the implementation of TPM (Total Productive Maintenance) and regular planned maintenance shut downs, we achieved a significant minimization of unplanned downtime within a few weeks.
By introducing 5S concepts, the production environment was optimally organized to avoid waste in motion.
According to the KAN BAN principle, the material supply to the production was organized to ensure an uninterrupted material supply.
Through SMED workshops we were able to minimize rest times enormously and thus increase the productive time at the bottlenecks.
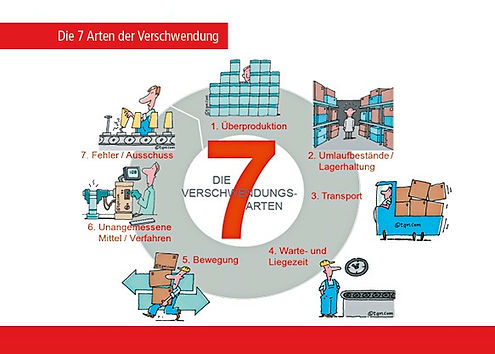